1:1 ratio double beam bed
Symmetrical double beams ensure even force distribution during processing, effectively correcting tilting caused by load on the beams, resulting in higher stability, reducing deformation caused by lateral forces, and maintaining stable accuracy during cutting.
View DetailsX-axis drive dual-drive dual-electric gap elimination
It adopts imported high-precision gears, racks, gearboxes, and linear guides, with a dual-drive dual-electric gap elimination structure. The displacement accuracy and synchronization accuracy of the dual drive are precisely controlled by the grating ruler and CNC system, achieving high-speed and high-precision operation of the gantry.
View DetailsQuadruple slide, dual-speed gear head
Meets the need for greater torque during cutting. The spindle head's center of gravity is evenly close to the center of the beam to achieve better motion accuracy and heavy cutting capacity. High-grade wear-resistant alloy resin sand castings are used and heat-treated to ensure the best dynamic response under maximum load. High-tensile cast material is used for excellent wear resistance.
View DetailsVertical and horizontal conversion tool magazine
Achieve efficient storage and management of a large number of tools, quickly change tools during processing, improve processing efficiency and accuracy, and save time for changing attachments and tools. The vertical and horizontal conversion makes tool changing more flexible and faster.
View DetailsHoneycomb structure, laterally widened design
Ultra-high rigidity structure: The base adopts a multi-layer wall reinforced rib design, using high-grade alloy wear-resistant castings, and undergoes tempering treatment and stress relief. The ultra-large column structure with a large beam support surface ensures optimal structural rigidity. Honeycomb structure, high strength, high heat dissipation rate, low deformation, and good vibration absorption
View DetailsFollow-up beam retainer and screw rod support
Effectively controls the distance between the two beams, reducing the impact of vibration during cutting on accuracy. Multiple screw rod brackets provide effective support for the screw rods, reducing screw rod sagging, uneven force, and providing continuous and stable torque output.
View DetailsProduct Advantages

1:1 symmetrical double beam design

Dual-drive dual-electric gap elimination

Quadruple slide, dual-speed gear head

Honeycomb structure, laterally widened design

High-strength column, telescopic hole

Vertical and horizontal conversion tool magazine



1:1 ratio double beam bed
The symmetrical double-beam design ensures even force distribution during processing, effectively correcting beam tilting under load, resulting in higher stability, reducing lateral and longitudinal force-induced compression deformation, maintaining stable accuracy during cutting, and ensuring long-lasting high-precision processing. Improves processing accuracy and thus increases production efficiency.



X-axis drive dual-drive dual-electric gap elimination
PANDK Rui double-beam gantry machining center adopts imported high-precision gears, racks, gearboxes, and linear guides, and uses a dual-drive dual-electric gap elimination structure. The displacement accuracy and dual-drive synchronization accuracy are precisely controlled by the grating ruler and CNC system, achieving high-speed and high-precision gantry operation. It provides hardware and software guarantees for continuous high-precision processing.



Quadruple slide, dual-speed gear head
Provides greater torque during cutting. The spindle head's center of gravity is evenly close to the center of the beam to achieve better motion accuracy and heavy cutting capacity. The spindle head uses high-grade wear-resistant alloy resin sand castings and is heat-treated to eliminate internal stress, ensuring the best dynamic response under maximum load. High-tensile cast material is used for excellent wear resistance. Combined with a 30/37kw spindle motor, it is absolutely simple and has geometric stability, providing a maximum torque of 2000NM, making it suitable for high-efficiency processing of medium and large workpieces.



Honeycomb structure, laterally widened design
Ultra-high rigidity structure: The base adopts a multi-layer wall reinforced rib design, using high-grade alloy wear-resistant castings, and undergoes tempering treatment and stress relief. The ultra-large column structure with a large beam support surface ensures optimal structural rigidity. Honeycomb structure, high strength, high heat dissipation rate, low deformation, and good vibration absorption. The bed and worktable are fixedly installed. The unique installation design scheme and multi-point, multi-area foundation fixation ensure the long-term planarity of the worktable, further improving the processing accuracy of the workpiece.



Effectively controls the distance between the two beams, reducing cutting vibration.
Equipped with a follow-up beam retainer and multiple screw rod supports, effectively controlling the distance between the two beams, reducing the impact of vibration during cutting on accuracy, and keeping the machine tool accuracy constant. Within a certain distance, multiple screw rod brackets provide effective support for the screw rods, reducing screw rod sagging, uneven force, and providing continuous and stable torque output.



Vertical and horizontal conversion tool magazine Four-axis control room
Achieve efficient storage and management of a large number of tools, quickly change tools during processing, improve processing efficiency and accuracy, and save time for changing attachments and tools. The vertical and horizontal conversion makes tool changing more flexible and faster. The anti-drop device effectively protects the personal safety of operators.
Superior Performance

Superior Performance
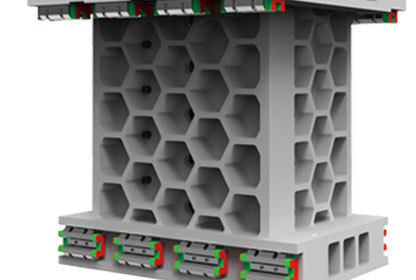
Honeycomb structure, reinforcing ribs, improved rigidity
Ultra-high rigidity structure: The base adopts a multi-layer wall reinforced rib design, using high-grade alloy wear-resistant castings, and is tempered and stress-relieved. The ultra-large column structure with a large beam support surface ensures optimal structural rigidity. Honeycomb structure, high strength, high heat dissipation rate, low deformation, good vibration absorption. The bed and worktable adopt fixed installation methods, and a unique installation design scheme with multi-point and multi-area fixation to the foundation. This effectively ensures that the worktable does not deform under heavy loads, and the castings adopt alloy wear-resistant castings. The resin sand molding is processed through multiple tempering and aging processes to ensure the long-term flatness of the worktable, further improving the processing accuracy of the workpiece.
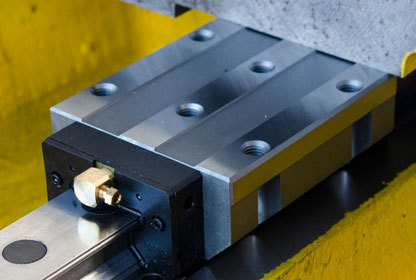
High rigidity guide rail, high precision screw
X\Y-axis guide rails adopt imported high-rigidity rolling guide rails, using internationally popular installation methods. The system has high rigidity, no creeping, and smooth movement within any feed rate range, from low speed to high speed. X-axis adopts high-precision rack transmission, Y, Z-axis adopts high-precision screw transmission. Z-axis adopts 450mm*450mm square slide, full-enclosed hard rail structure. The spindle head adopts double oil cylinder pressure counterweight, and its center line is close to the center of gravity of the spindle head. The spindle is located at the optimal position in the center of the spindle motor, Z-axis screw, and double symmetrical counterweight hydraulic cylinder, which can eliminate the generation of unbalanced torque, ensuring the accuracy of micro-feed and long-term processing.
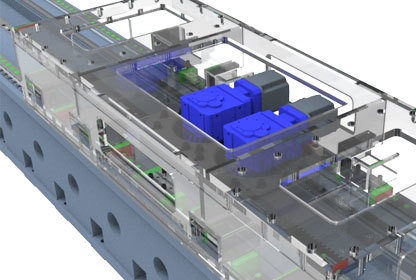
X-axis drive
It adopts imported high-precision gears, racks, gearboxes, and linear guides, with a dual-drive dual-electric gap elimination structure. The displacement accuracy and synchronization accuracy of the dual drive are precisely controlled by the grating ruler and CNC system, achieving high-speed and high-precision operation of the gantry.
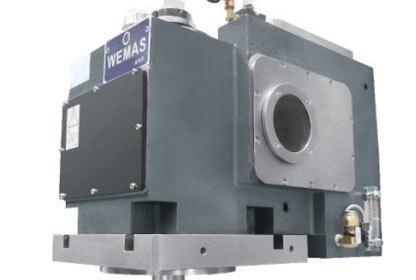
Gear spindle, dual-speed gearbox
The spindle head center of gravity is evenly close to the center of the beam to achieve better motion accuracy and heavy cutting ability. The spindle head adopts high-grade wear-resistant alloy resin sand castings, and is heat-treated to eliminate internal stress, ensuring the best dynamic response under maximum load. It adopts high-tensile cast material with excellent wear resistance. Gear spindle 3000rpm\4000RPM\6000rpm, high rigidity, with 30\37kw spindle motor, absolutely simple and with excellent geometric stability, providing a maximum torque of 2000NM, therefore suitable for high-efficiency processing of medium and large workpieces.
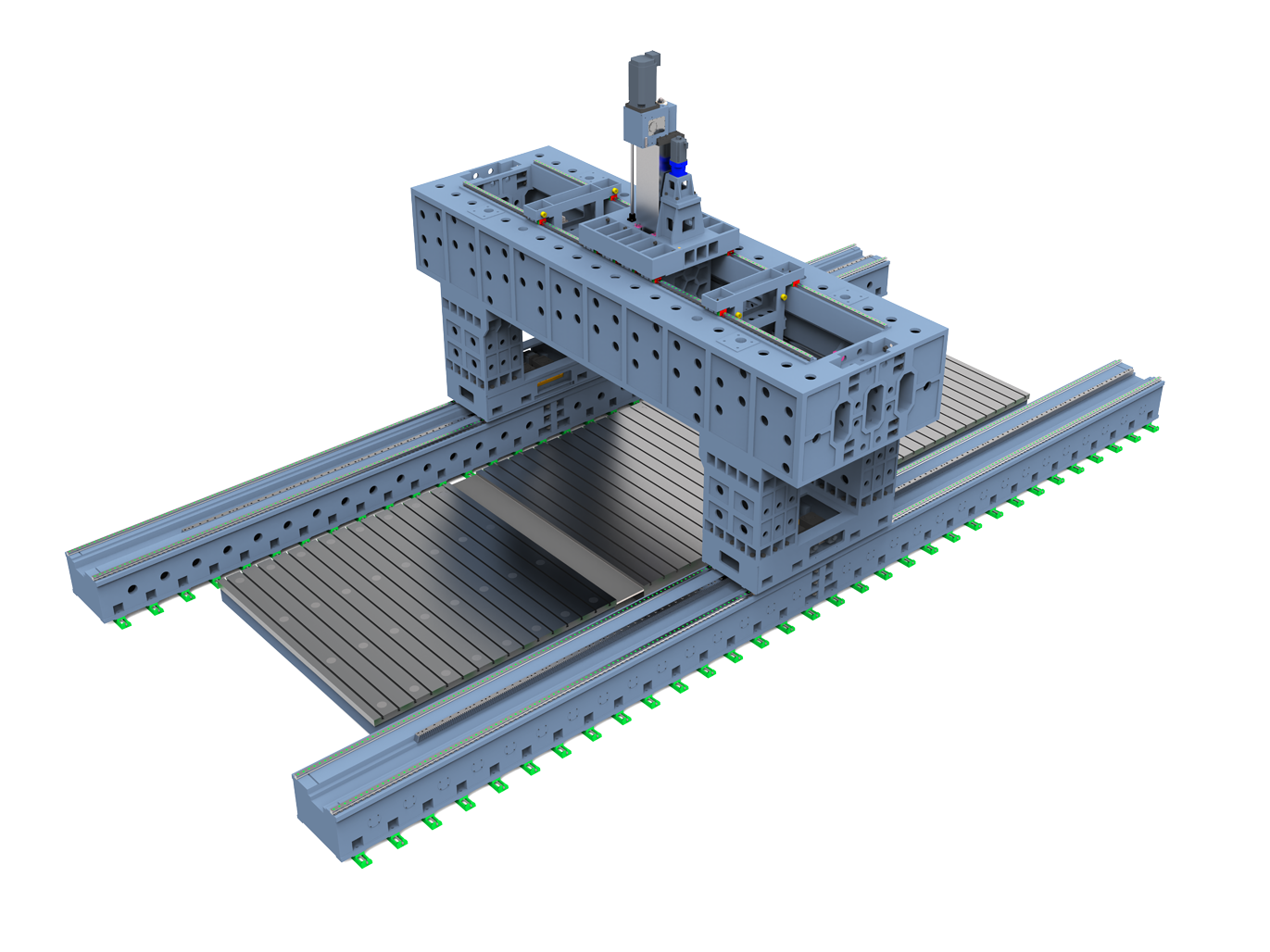
Quality service
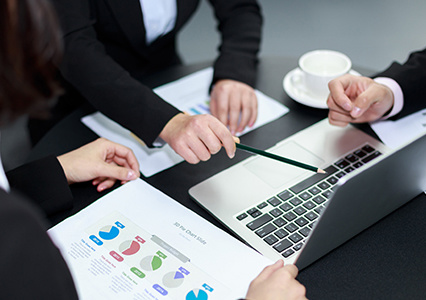
01
Product customization
According to the customer's workpiece processing needs, customize the machine tool processing stroke, expand the multi-functional worktable, and optionally select automatic tool setting, fourth axis and other machine tool accessories.
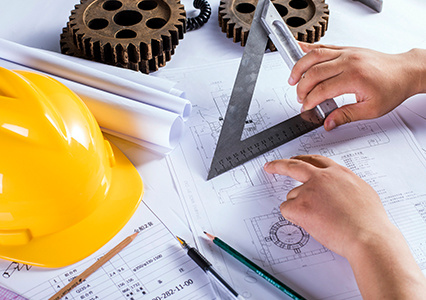
02
Product debugging and delivery
The seller's technicians will go to the end user's factory to install and debug the equipment. The end user should notify the seller to install and debug the equipment within 5 days after the equipment arrives at the factory.
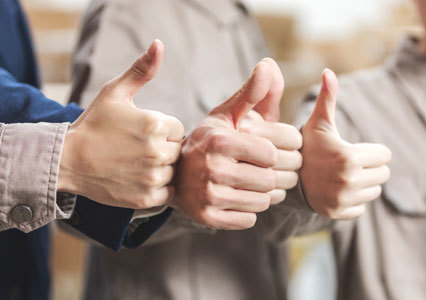
03
Product operation and technology training
On-site training at the end user's factory. The seller's technicians will go to the end user's factory to install and debug the equipment, and conduct training on machine tool operation and maintenance at the same time.
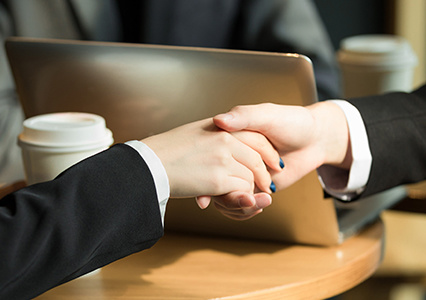
04
Perfect after-sales service
Free warranty for one year from the date of mechanical self-acceptance. However, if the damage is caused by improper use by the user unit, it is not within the above free warranty period, and the user must pay all repair costs.
Exploration and Innovation, Cooperation and Win-Win
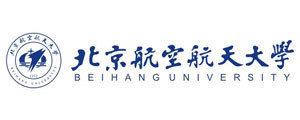
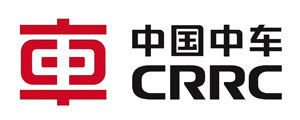
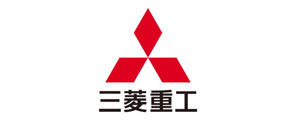
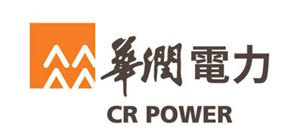
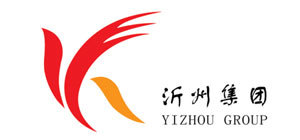
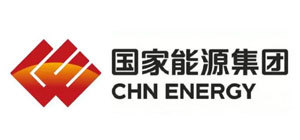
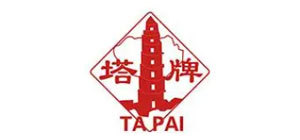
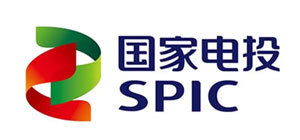
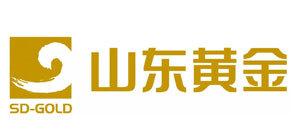
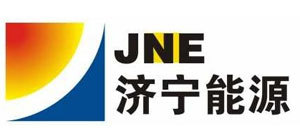
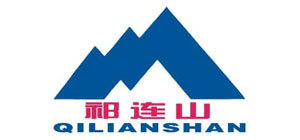
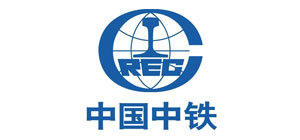
Quality Product Recommendation